PTFE Compression Molding: Applications and Benefits
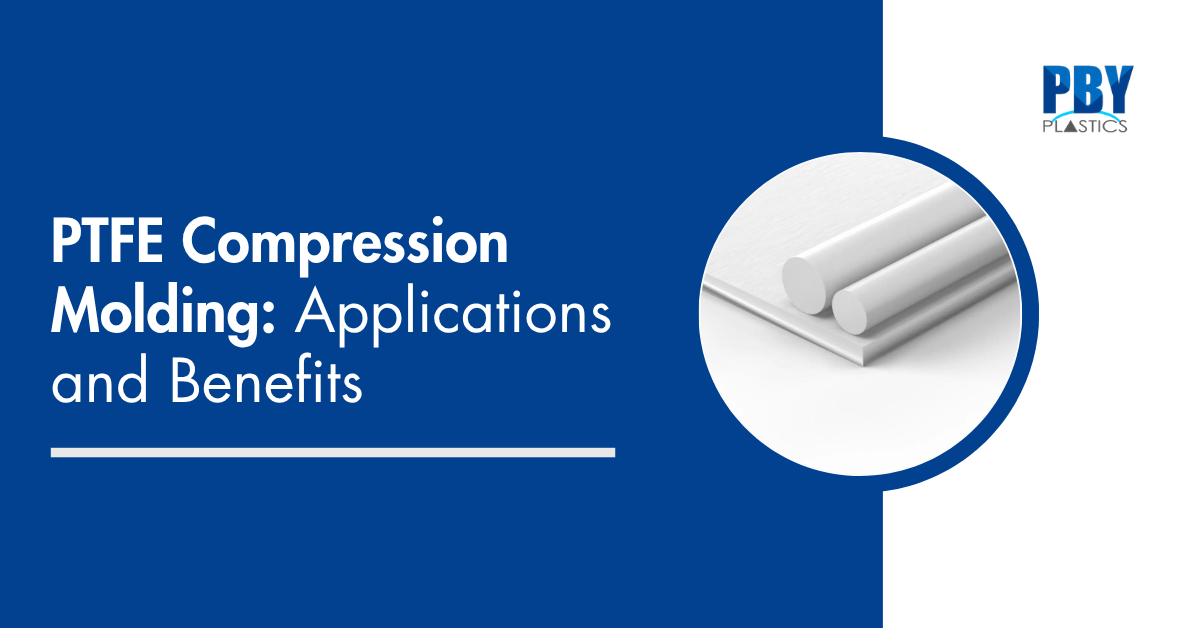
Polytetrafluoroethylene (PTFE) is a remarkable polymer that has earned its place as a key material in industries requiring exceptional performance under extreme conditions. Known for its chemical resistance, high-temperature tolerance, and low friction coefficient, PTFE sets the standard for reliability and durability. Its adaptability and unique physical properties have made it indispensable across a wide range of applications. Among the methods used to shape and process PTFE, compression molding stands out as a manufacturing technique that ensures precision, uniformity, and customization.
This article explores PTFE's fascinating history, the technical aspects of compression molding, its unparalleled industrial applications, and the future developments that will continue to enhance its versatility.
A Brief History and Development of PTFE
PTFE was discovered in 1938 by Dr. Roy Plunkett, a researcher working for DuPont. While experimenting with tetrafluoroethylene gas, Plunkett stumbled upon a white waxy substance that would later revolutionize material science. PTFE's unique combination of chemical inertness and thermal stability immediately sparked interest.
The polymer gained widespread use during World War II as a coating for equipment in the Manhattan Project. By the 1950s, DuPont introduced PTFE under the trademark "Teflon," bringing it to commercial and domestic markets. Over the years, refinements in manufacturing techniques, including the development of compression molding, allowed PTFE to cement itself as a critical component in industrial and technological advancements.
The Compression Molding Process for PTFE
Compression molding is a versatile and efficient method for shaping PTFE into high-performance components. Unlike melt-processible polymers, PTFE cannot be injection molded owing to its high melt viscosity. Instead, it is shaped using compression molding, which involves compacting pre-sintered or granular PTFE powder into a mold under high pressure.
Steps in PTFE Compression Molding:
1. Preparation- PTFE powder is prepared and loaded into a mold cavity.
- The powder is compressed under pressures ranging from 3,000 to 10,000 psi, depending on the desired density and application.
- The compressed preform is heated in an oven to a temperature over 680°F (360°C)—just above PTFE’s melting or gel point. This fuses the particles into a cohesive structure, preserving its unique properties.
- The molded part is gradually cooled to avoid internal stresses and defects.
Equipment Used:
Compression molding requires specialized equipment, including hydraulic presses capable of high-pressure cycles to ensure accuracy and consistency.
Challenges:
- Achieving uniformity in large or complex components can be challenging due to potential voids or uneven density.
- Controlling shrinkage during the sintering and cooling stages requires precise calibration to maintain dimensional accuracy.
Despite these hurdles, compression molding remains the preferred method for manufacturing PTFE components tailored to precise industrial demands.
Diverse Applications of PTFE Compression Molding
PTFE's versatility extends across industries from aerospace to healthcare, making it one of the most widely used synthetic materials in modern history. Its properties enable functionality and reliability, especially in extreme or corrosive environments.
1. Aerospace Industry
Application: PTFE seals, gaskets, and bearings are essential to aircraft and spacecraft performance.
Benefits:
- High temperature resistance allows PTFE components to function in engine systems.
- Lightweight properties contribute to fuel efficiency, a critical consideration in aerospace design.
2. Electronics Industry
Application: PTFE serves as an insulating material for wires, cables, and circuit boards.
Benefits:
- Exceptional dielectric properties and thermal characteristics ensure longevity.
- PTFE prevents signal loss and withstands high-voltage stress in advanced electronics.
3. Automotive Industry
Application:
- Common in fuel system components, such as gaskets and seals.
- Used in transmission systems for its low friction coefficient.
Benefits:
- PTFE's chemical inertness ensures durability in environments with constant exposure to fuels, oils, and lubricants.
- Its low friction coefficient.
4. Chemical Processing
PTFE is invaluable in the chemical industry, where components like valve liners, pipe linings, and containers are exposed to corrosive agents.
Case Study:
- A chemical plant that switched to PTFE-lined pipes experienced a 70% reduction in downtime caused by corrosion, saving significant maintenance costs over a five-year period.
5. Food and Textile Industries
Application:
- PTFE is used in food processing equipment as liners, gaskets, and conveyor belts due to its non-stick properties.
- Similarly, in textiles, it is used in coating machines to ensure smooth fabric transport.
Benefits:
- Its non-reactive surface adheres to food and textile safety regulations, preventing contamination or adhesion of materials.
6. Medical and Healthcare Industry
The biocompatibility of PTFE makes it a trusted material for implantable devices, such as vascular grafts and surgical tools. Precision compression molding ensures all safety and quality requirements are met.
Ongoing Improvements in PTFE Sustainability
While PTFE boasts durability and performance, its environmental footprint is a subject of ongoing improvement. While non-biodegradable, its long lifespan reduces waste compared to alternative materials. Efforts to enhance sustainability include:
- Recycling Initiatives:
- Development of processes to reuse and repurpose PTFE scrap.
- Eco-friendly Sintering Techniques:
- Reducing energy consumption by incorporating energy-efficient ovens during manufacturing.
- Extended product lifecycles ensure efficient resource use, further emphasizing PTFE's role in sustainable engineering.
Future Trends and Innovations in PTFE Manufacturing
Exciting developments are on the horizon for PTFE compression molding and applications:
1. Automation in Compression Molding
- Integration of sensors and artificial intelligence for real-time defect detection will enhance the reliability and consistency of manufacturing processes.
2. Hybrid PTFE Composites
- Reinforcing PTFE with short carbon nanotubes, graphene, Nomex, PEEK, is emerging as a way to tailor specific properties like increased strength, improved thermal conductivity or tribological wear.
3. Emerging Industries
- PTFE is becoming increasingly relevant in renewable energy applications, such as wind and solar energy systems, thanks to its chemical and environmental resistance.
4. Miniaturization in Electronics
- PTFE's ability to meet tight dimensional tolerances ensures its relevance in the production of micro-electronics and next-generation computing systems.
A Comprehensive Summary of PTFE Compression Molding
PTFE compression molding remains a fundamental manufacturing process, enabling the production of customized, high-performance components for applications demanding unmatched durability. Its low stick, high-temperature stability, and chemical resistance qualities provide a solution for extreme industrial, medical, and automotive challenges.
Key takeaways:
- PTFE’s unique properties make it versatile across industries, from packaging valves in chemical plants to implants in healthcare.
- Compression molding ensures tight tolerances and uniform density, critical for end-use performance.
- Advances in automation and sustainability are expanding the scope of PTFE’s applications, keeping it at the cutting edge of material science.
Given its unparalleled combination of properties and the versatility of compression molding, PTFE continues to play a pivotal role in shaping the technological and industrial advancements of our time. Whether in aerospace systems or tiny microprocessors, PTFE is the unsung hero every industry depends on.
Explore the full range of high-performance materials—visit our Materials page to learn more.