Why PFA Compression Molding is Essential for Chemical Resistance and Industrial Resistance
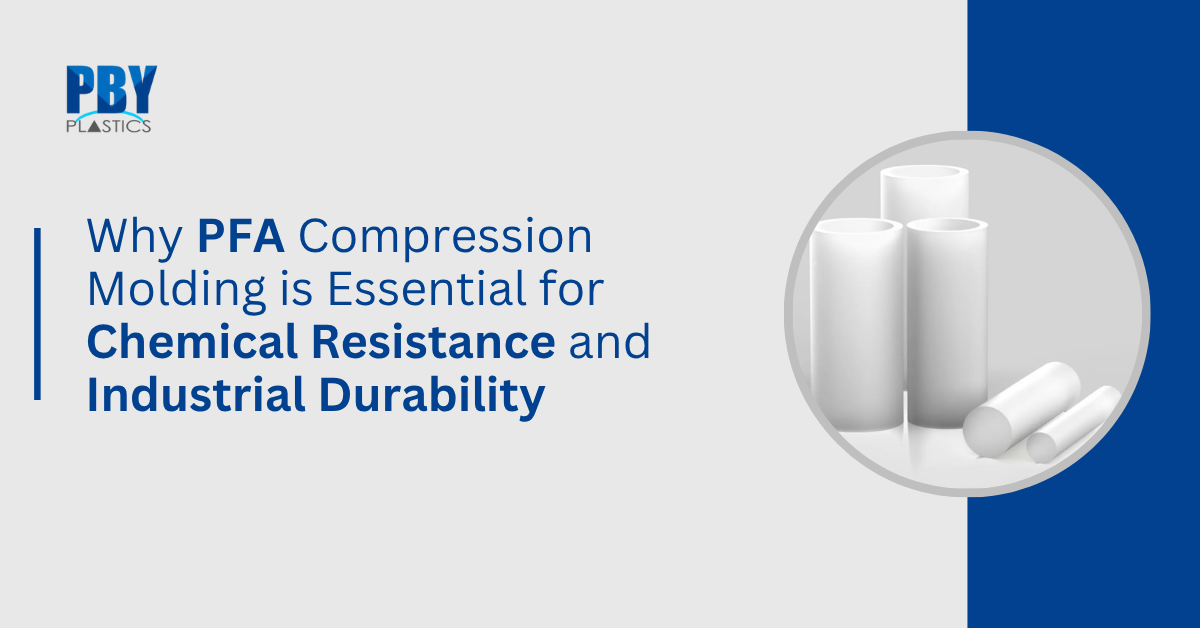
Industries operating in high-stress environments demand materials capable of withstanding extreme temperatures, corrosive chemicals, and mechanical forces—all while maintaining long-term performance. This is where perfluoroalkoxy (PFA) polymers come in. Known for their exceptional properties, PFA isn't just a material of choice—it's a benchmark for reliability and durability. When combined with compression molding, its true potential is unlocked, establishing a foothold in critical applications across multiple industries.
This article will take a deeper look into PFA, its unique capabilities, the intricacies of the compression molding process, and its role in shaping the future of industrial reliability.
A Closer Look at PFA and Its Development
PFA was introduced in 1973 as an innovation in the realm of fluoropolymers, combining the chemical resistance and thermal stability of polytetrafluoroethylene (PTFE) with the advantage of being melt-processable. This enabled industries to fabricate complex shapes and components that were previously difficult or cost-prohibitive with PTFE.
PFA is created through the copolymerization of tetrafluoroethylene (TFE) and perfluoroalkyl vinyl ethers (PAVE). This structure gives it its defining characteristics, such as:
- A melting point range of 305-315°C.
- Exceptional chemical resistance and thermal stability.
- Mechanical durability with a tensile strength of minimum 3600 psi and a specific gravity around 2.16.
PFA distinguishes itself from PTFE with a viscosity more than one million times lower, enabling precise molding for complex components. These features have cemented PFA's position in applications where materials must perform flawlessly under harsh conditions.
Compression Molding and Its Technical Mastery
Compression molding is a key process that maximizes PFA's potential. This technique involves heating PFA above its melting point, placing it into a heated die , and applying high pressure to shape it. Once cooled, the result is a precise, high-strength component that retains all the desirable properties of the polymer.
Key Steps in Compression Molding:
- Preheating the mold to avoid temperature shock when introducing the polymer.
- Melting the polymer, at an adequate processing temperature.
- Applying controlled high pressure to compress the polymer into the mold cavity.
- Cooling the part under pressure to ensure dimensional stability and avoid defects.
Equipment and Challenges
This process requires specialized presses with independent heating and cooling systems. Many setups use several platen presses, with one or more presses electrically heated.
Challenges in compression molding include:
- Ensuring accurate temperature control to prevent polymer degradation.
- Addressing dimensional shrinkage during cooling can vary based on mold design, pressure application, and type of PFA resin.
- Achieving uniform distribution of properties for components with complex geometries.
Despite these challenges, compression molding remains one of the most effective ways to fabricate PFA components, especially for applications requiring tight tolerances and long-term durability.
Real-World Applications of PFA
PFA’s unique properties translate into practical solutions across various industries. It is particularly valued in environments where other materials fail due to chemical degradation, excessive wear, or thermal fluctuations.
Chemical Processing
PFA is the go-to material in chemical plants due to its compatibility with aggressive substances. Piping systems, valve linings, and storage tanks are frequently lined with PFA to prevent damage from acids, bases, and organic solvents. For example:
- Case Study: A chemical producer switched to PFA-lined pumps and significantly reduced downtime caused by pump failures from corrosive liquids like sulfuric acid.
Semiconductor Manufacturing
The semiconductor industry relies heavily on the high purity and chemical inertness of PFA. It is used in wafer carriers, etching chambers, and tubing systems to transport ultra-pure chemicals without the risk of contamination—a critical requirement in microchip fabrication.
Automotive Sector
PFA's resistance to heat and chemicals makes it a practical choice for under-the-hood applications, such as fuel systems. These components operate in environments with prolonged exposure to extreme temperatures and aggressive fluids, which PFA handles with ease.
Aerospace Applications
Aerospace engineers rely on PFA for protective coatings, wires, and cable insulation. Its ability to withstand extreme temperature fluctuations—ranging from cryogenic conditions to high heat—ensures safe operation in space and aviation environments.
Electrical and Electronics
With a dielectric strength of 19.7 kV/mm and volume resistivity exceeding 10¹⁸ Ω·cm, PFA excels in insulation applications. Its low dissipation factor and arc resistance make it indispensable for high-voltage electrical systems and delicate electronics.
Protective Coatings
From chemical reactors to storage tanks, PFA coatings offer unbeatable resistance to permeation and product contamination. Their non-stick properties also simplify maintenance, reducing downtime for cleaning and repair.
Environmental Impact and Sustainability
While PFA is favored for its chemical inertness and long service life, questions about its lifecycle environmental impact are increasingly relevant. Manufacturing involves high energy consumption due to the elevated temperatures required for processing. However, PFA's durability and low maintenance needs often offset these initial costs by reducing waste and extending the lifespan of industrial equipment.
Efforts to improve the sustainability of PFA production include:
- Exploring eco-friendly finishing processes to minimize emissions during polymerization.
- Developing recycling initiatives for PFA waste, where it can be repurposed into secondary applications.
- Innovating fabrication methods such as roto lining to reduce material waste.
Future Trends in PFA and Compression Molding
The demand for high-performance materials like PFA continues to grow across industries. Advances in material science and processing techniques promise to push the boundaries of what PFA can achieve.
Key Innovations on the Horizon:
- Automation in Compression Molding:
Automated systems with real-time temperature and pressure monitoring will improve efficiency and consistency in PFA component manufacturing.
- Hybrid Materials:
Combining PFA with other polymers or fillers (e.g., carbon fiber) can enhance mechanical properties and expand application possibilities.
- Green Manufacturing Practices:
The industry is shifting toward sustainable polymerization processes that reduce energy consumption and environmental impact.
- Emerging Applications:
PFA is making inroads into biomedical devices where its biocompatibility, sterilization resistance, and chemical inertness offer significant advantages.
A Comprehensive Summary of PFA's Benefits
PFA stands out as a material of the future, offering unmatched thermal stability, chemical resistance, and mechanical reliability in extreme environments. Its unique combination of properties enables applications that demand precision, durability, and long service life.
Through compression molding, manufacturers unlock the full potential of PFA, creating components with tight tolerances and high performance. This process plays a vital role in ensuring that PFA components are reliable under the harshest conditions, from semiconductor fabrication labs to aerospace applications.
While challenges remain—such as improving sustainability and further refining process efficiency—the future of PFA looks bright. Industries worldwide continue to trust this remarkable material to meet the most demanding requirements, standing as a testament to its versatility and value. With ongoing advancements, PFA and its processing techniques will undoubtedly drive innovation and reliability for decades to come.
Want to learn more about PFA and how it supports your processes? Visit our Materials page for detailed data and explore what sets PBY apart.